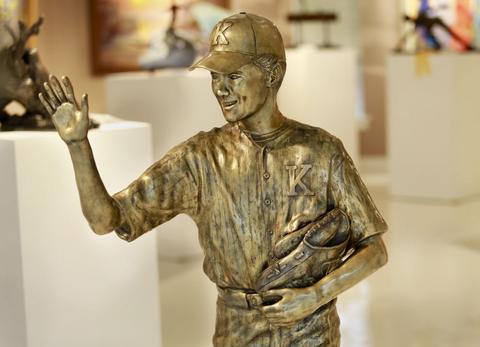
Bronze Baseball Sculpture Coming to Virginia Beach Park
January 1, 2015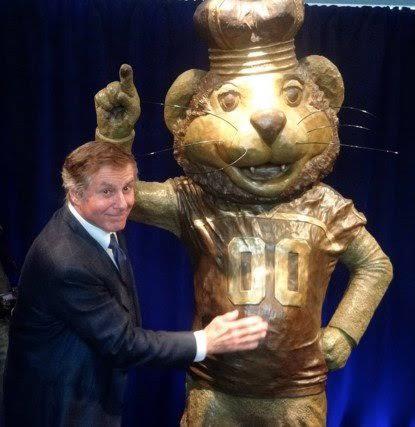
National Art Museum of Sport – Artist of the Month December 2015 – Richard Stravitz
December 1, 2015Have you ever wondered about the Lost Wax Casting Process? The “lost wax” method of casting bronze is an ancient craft at least 5,000 years old! It remains essentially unchanged but has been improved with modern technology.
The artist sculpts a model in clay, or wax, of exactly the image he wishes to create. In doing so, the artist must anticipate mold making, welding joints, etc., so that future steps in the process are as easy as possible.
Next a rubber and/or plaster mold is made of every part of the sculpture. Sometimes there is one piece, sometimes many. After the mold is made, the clay or wax model is of no further use and is usually recycled.
Into the mold, hot wax is brushed and poured to form a hollow wax pattern identical to the original mold. For every bronze that will be made there must be a wax pattern.
After wax gates, vents, and channels are attached to the wax pattern, it is ready to be “invested.” Investing is a process of building a mold of a refractory material around and into the hollow wax pattern. This is accomplished by alternately dipping the wax into a liquid silica and then powdered silica, allowing each coat to dry for several hours. After about a week the mold is built up to the thickness needed to hold molten bronze.The wax pattern, now encased in a silica mold, is then placed in a 1500 degree oven and the wax is melted out, leaving a hollow silica mold ready to receive the molten bronze.
The mold cools and after inspection for cracks, is inverted (with the opening pointing up) in the same oven and reheated. At the same time, bronze ingots are melted (2000 degrees F) and the molten bronze is poured into the hot silica mold.
Once again the piece is allowed to cool thoroughly, then the mold is removed with hammers and a sandblaster. The bronze sprues and vents are removed and the casting remains. If more than one piece is involved in the sculpture, the parts are welded together and the resulting seams removed with careful grinding and sanding.
The bronze is ready for the final finish, a patina, after a final sandblasting or glassbeading. Patinas are created by applying liquid chemicals to the surface of a bronze after it is heated with a blow torch. Under heat, these chemicals react with the copper content of the bronze alloy to give a controlled oxidation. Colors can vary according to the intensity of the heat and the chemicals used. Usually many coats are applied until the desired color is obtained.
The final step is the application of several coats of wax or sealer to enrich the color and protect the bronze.
Check out this video to see just how intricate & amazing the art is! https://youtu.be/jmMoG3tOxU8